Day :
- Materials Science and Engineering
Location: Webinar
Session Introduction
Sidpouita Mathilde Koudougou
Polytechnic School of Ouagadougou
Title: Thermomechanical response of bituminous pavements to hot and dry tropical weather conditions
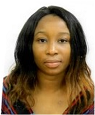
Biography:
Koudougou Sidpouita Mathilde obtained her scientific baccalaureate in 2005 in Ouagadougou, Burkina Faso, followed by a Bachelor's degree in Mechanical Physics and a Master's degree in Complex Systems with a specialization in Complex Fluids and Divided Media at the Faculty of Sciences of the University of Paris Saclay in France from 2008 to 2011. Her various internships and professional experiences in academia and industry (Psa Peugeot Citroen, Colas etc.) in the field of Research and Innovation in France have fuelled her desire to pursue a career in research. This is how she carried out her PhD thesis in Applied Physics specialising in thermophysics/complex materials from 2016 - 2020 at the Joseph Ki-Zerbo University of Ouagadougou under the supervision of Professor David Yemboini Kader TOGUYENI within the Laboratory of Environmental Physics and Chemistry. Her research work earned her an award at a scientific seminar dedicated to doctoral students and young doctors, conducted by the doctoral schools of the Joseph Ki-Zerbo University. Since June 2021, she has been a research assistant in physics at the Ecole Polytechnique de Ouagadougou.
Abstract:
The main objective of this paper is to propose a two-dimensional (2D) model of temperature distribution and deformations of bituminous pavements under extreme climatic conditions in Burkina Faso (heat wave) using the COMSOL Multiphysics software. This model takes into account the geometry, the hourly weather conditions (solar radiation, air temperature, air humidity, dew point temperature, wind speed) as well as the temperature dependence of the mechanical parameters (modulus of elasticity, Poisson's ratio), thermo physical properties (thermal conductivity, diffusivity) of the materials. The results obtained show that it is possible to identify, for periods of the day, the existence of non-linear and permanent deformations in the surface layers of the pavements. The meteorological factor, namely temperature, was found to be very important in the choice of bitumen used for asphalt pavement construction in tropical areas.
Tuba Kizilirmak
University of Sheffield, UK
Title: Additive manufacturing of Ti6Al4V lattices for spinal fusion cages
Biography:
Tuba Kizilirmak has received his bachelor degree from Eskisehir Technical University in Turkey. She studied barite mineral in final year research project. The research title was High Purity Powder Synthesis from Barite Mineral. She achieved to complete master degree at University of Leicester. She gained experience on modeling techniques such as SolidWorks, COMSOL, MATLAB. She completed master thesis on molecular dynamics simulation of particle interactions. This research used the technology of LAMMPS simulation program. She is currently doing PhD research at University of Sheffield. Her research project title is Additive Manufacturing of Ti6Al4V Lattices for Spinal Fusion Cages. Her research project covers the topic of biomaterials.
Abstract:
Selective Laser Melting is rapid prototyping technique which enables prompt modelling of parts with high bulk density on the base of individual three dimensional data. In this study, we will test the SLM produced samples with on the basis of Ti6Al4V alloy for its applicability in spinal fusion cages. Great modulus of spinal fusion cages causes an accumulation of stress on implant and this cause stress shielding problem which results in long term damage to vertebral bodies. This study considers the effect of stress shielding on the bone-implant interaction and optimize the stiffness of titanium scaffolds. When the loads on the implants could not be transferred to the bone due to the higher elastic modulus of the implant than bone, so stress shielding effect appears on the interface of bone and implant. Optimization of cell topologies of titanium scaffolds will optimize the stiffness and give a value close the stiffness of cancellous bone. Compressive tests will prove that the stiffness of the porous structures. Both experimental and modeling of compression test was done to compare both results. This study will aim to understand the effect of pore geometry on the in vitro biological behavior of bone cells seeded on selective laser-melted Ti6Al4V bone scaffolds. Pentamode lattice structure was selected with 70%, 80% and 90% porosities. Produced scaffolds were characterized by two-dimensional optical microscopy and Scanning Electron Microscopy (SEM). 3-Dimensional cell culture test will be practiced with MLO-A5 cells on selected titanium scaffolds. This test is for the identification of the best unit cell model and pore size of titanium scaffolds for the enhanced bone matrix production and facilitated long-term static culture.
Osman Adiguzel
Firat University,Turkey
Title: Dual thermoelastic and superelastc characterization of shape memory alloys
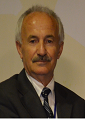
Biography:
Some materials take place in class of smart materials with adaptive properties and stimulus response to the external changes. Shape memory alloys take place in this group, due to the shape reversibility and capacity of responding to changes in the environment. These alloys have a peculiar property called shape memory effect. Shape memory effect is initiated by cooling and stressing treatments in material in bulk level and performed thermally on heating and cooling after first treatments. Therefore, this behavior is called thermoelasticity. These alloys exhibit another property called superelasticity, which is performed by stressing and releasing at a constant temperature in the parent austenite phase region. Shape memory effect is result of successive thermal and stress induced martensitic transformations. Thermal induced martensitic transformation occurs on cooling along with lattice twinning, with which ordered parent phase structures turn into twinned martensite structures, and twinned structures turn into detwinned martensite structures by means of strain induced martensitic transformation with deformation in martensitic state. Thermal transformations occur with cooperative movement of atoms by means of lattice invariant shears in <110>-type directions on a {110} - type plane of austenite matrix.
Superelasticity is performed in only mechanical manner. These alloys can be deformed in parent phase region just over austenite finish temperature and recover the original shape on releasing the applied stress. Superelasticity is also result of stress induced martensitic transformation which occurs only by mechanical stress at a constant temperature. With this stress, parent austenite phase structures turn into the fully detwinned martensite. Superelasticity exhibits normal elastic material behaviour, but it is performed in non-linear way, unlike normal elastic materials. Loading and unloading paths are different, and hysteresis loop refers to the energy dissipation.
Copper based alloys exhibit this property in metastable b - phase region, which has bcc-based structures at high temperature parent phase field. Lattice invariant shear and twinning is not uniform in copper alloys and they give rise to the formation of unusual layered complex structures, like 3R, 9R or 18R structures depending on tha stacking sequences, with lattice twinning.
In the present contribution, x-ray diffraction and transmission electron microscopy studies were carried out on two copper based CuZnAl and CuAlMn alloys. X-ray diffraction profiles and electron diffraction patterns exhibit super lattice reflections inherited from parent phase due to the displacive character of martensitic transformation. Specimens of these alloys aged at room temperature in martensitic condition, and a series of x-ray diffractions were taken duration aging at room temperature. Reached results show that diffraction angles and peak intensities change with aging time at room temperature, and this result leads to the rearrangement of atoms in diffusive manner.
Abstract:
Some materials take place in class of smart materials with adaptive properties and stimulus response to the external changes. Shape memory alloys take place in this group, due to the shape reversibility and capacity of responding to changes in the environment. These alloys have a peculiar property called shape memory effect. Shape memory effect is initiated by cooling and stressing treatments in material in bulk level and performed thermally on heating and cooling after first treatments. Therefore, this behavior is called thermoelasticity. These alloys exhibit another property called superelasticity, which is performed by stressing and releasing at a constant temperature in the parent austenite phase region. Shape memory effect is result of successive thermal and stress induced martensitic transformations. Thermal induced martensitic transformation occurs on cooling along with lattice twinning, with which ordered parent phase structures turn into twinned martensite structures, and twinned structures turn into detwinned martensite structures by means of strain induced martensitic transformation with deformation in martensitic state. Thermal transformations occur with cooperative movement of atoms by means of lattice invariant shears in <110>-type directions on a {110} - type plane of austenite matrix.
Superelasticity is performed in only mechanical manner. These alloys can be deformed in parent phase region just over austenite finish temperature and recover the original shape on releasing the applied stress. Superelasticity is also result of stress induced martensitic transformation which occurs only by mechanical stress at a constant temperature. With this stress, parent austenite phase structures turn into the fully detwinned martensite. Superelasticity exhibits normal elastic material behaviour, but it is performed in non-linear way, unlike normal elastic materials. Loading and unloading paths are different, and hysteresis loop refers to the energy dissipation.
Copper based alloys exhibit this property in metastable b - phase region, which has bcc-based structures at high temperature parent phase field. Lattice invariant shear and twinning is not uniform in copper alloys and they give rise to the formation of unusual layered complex structures, like 3R, 9R or 18R structures depending on tha stacking sequences, with lattice twinning.
In the present contribution, x-ray diffraction and transmission electron microscopy studies were carried out on two copper based CuZnAl and CuAlMn alloys. X-ray diffraction profiles and electron diffraction patterns exhibit super lattice reflections inherited from parent phase due to the displacive character of martensitic transformation. Specimens of these alloys aged at room temperature in martensitic condition, and a series of x-ray diffractions were taken duration aging at room temperature. Reached results show that diffraction angles and peak intensities change with aging time at room temperature, and this result leads to the rearrangement of atoms in diffusive manner.